Q2. The level of liquid in a vessel is controlled by pure proportional control. The controller acts on a valve on the outlet stream by means of an analogue current signal in the range 4-20 mA. The valve stem position responds linearly to the current over the range 0-100% and for this installed valve it is known that the % of max flow is roughly equal to the % stem position (c.f. course notes p34, Fig 23). The maximum flowrate through the valve is 100 m³ hr:¹. At an initial steady-state condition, the level in the tank is at its set-point and the flow rates into and out of the tank are both 50 m³ hr¹. After a step-change disturbance in the inlet flowrate of 5 m³ hr¹, the process response results in a steady-state offset of 50 cm in the tank level. a) Calculate the gain of the controller (in mA/m) b) How should the gain be altered to limit level changes to ±1 m when the inlet flowrate may vary between 20 and 80 m³hr¹¹.
Q2. The level of liquid in a vessel is controlled by pure proportional control. The controller acts on a valve on the outlet stream by means of an analogue current signal in the range 4-20 mA. The valve stem position responds linearly to the current over the range 0-100% and for this installed valve it is known that the % of max flow is roughly equal to the % stem position (c.f. course notes p34, Fig 23). The maximum flowrate through the valve is 100 m³ hr:¹. At an initial steady-state condition, the level in the tank is at its set-point and the flow rates into and out of the tank are both 50 m³ hr¹. After a step-change disturbance in the inlet flowrate of 5 m³ hr¹, the process response results in a steady-state offset of 50 cm in the tank level. a) Calculate the gain of the controller (in mA/m) b) How should the gain be altered to limit level changes to ±1 m when the inlet flowrate may vary between 20 and 80 m³hr¹¹.
Introduction to Chemical Engineering Thermodynamics
8th Edition
ISBN:9781259696527
Author:J.M. Smith Termodinamica en ingenieria quimica, Hendrick C Van Ness, Michael Abbott, Mark Swihart
Publisher:J.M. Smith Termodinamica en ingenieria quimica, Hendrick C Van Ness, Michael Abbott, Mark Swihart
Chapter1: Introduction
Section: Chapter Questions
Problem 1.1P
Related questions
Question

Transcribed Image Text:Q2. The level of liquid in a vessel is controlled by pure proportional control. The controller acts on a
valve on the outlet stream by means of an analogue current signal in the range 4-20 mA. The valve
stem position responds linearly to the current over the range 0-100% and for this installed valve it is
known that the % of max flow is roughly equal to the % stem position (c.f. course notes p34, Fig 23).
The maximum flowrate through the valve is 100 m³ hr:¹.
At an initial steady-state condition, the level in the tank is at its set-point and the flow rates into and
out of the tank are both 50 m³ hr¹.
After a step-change disturbance in the inlet flowrate of 5 m³ hr¹, the process response results in a
steady-state offset of 50 cm in the tank level.
a) Calculate the gain of the controller (in mA/m)
b) How should the gain be altered to limit level changes to ±1 m when the inlet flowrate may
vary between 20 and 80 m³hr¹.

Transcribed Image Text:Q1. Advantages and disadvantages of using control actions in these combinations were outlined in
the lecture and are covered in detail in the lecture notes.
There was a lot of discussion of the concept of steady-state error for pure proportional control.
Remember that this can be understood by considering the control algorithm when only the
proportional part is present: c.a. = Kce + Bias
Consider a step disturbance to the flow in to a tank. When steady-state is reached, the flow out of
the tank should be the same as the flow in. This is largely achieved by having the exit valve open a
bit wider. To open the valve wider, we need a different control signal compared to the initial one
(since the bias is constant by definition). In pure proportional control this can only exist when there
is a finite error at steady state.
Q2. It was useful to start by writing down the control algorithm for pure proportional control.
c.a. Kçe + Bias
Following the comments on Q1 above, the change in the control signal required to accommodate
the additional flow corresponds to a steady-state error.
We can relate the change in flowrate to a change in the control signal (in mA) given the information
provided about the installed control valve.
Since we're told the corresponding steady-state error (in m), we're able to calculate the gain (in
mA/m). (note that this gain is strictly the product of the controller gain and the instrument gain).
For an increase of 5 m³ hr¹ in outlet flowrate, the valve must move by 5% of its full range
corresponding to a change in the control signal of (20-4)*0.05 = 0.8 mA.
Numerical answers: a) 1.6 mA m³¹; b) 4.8 mA m²¹.
Expert Solution

This question has been solved!
Explore an expertly crafted, step-by-step solution for a thorough understanding of key concepts.
Step by step
Solved in 4 steps with 3 images

Recommended textbooks for you
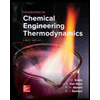
Introduction to Chemical Engineering Thermodynami…
Chemical Engineering
ISBN:
9781259696527
Author:
J.M. Smith Termodinamica en ingenieria quimica, Hendrick C Van Ness, Michael Abbott, Mark Swihart
Publisher:
McGraw-Hill Education
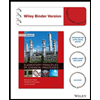
Elementary Principles of Chemical Processes, Bind…
Chemical Engineering
ISBN:
9781118431221
Author:
Richard M. Felder, Ronald W. Rousseau, Lisa G. Bullard
Publisher:
WILEY
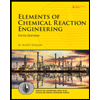
Elements of Chemical Reaction Engineering (5th Ed…
Chemical Engineering
ISBN:
9780133887518
Author:
H. Scott Fogler
Publisher:
Prentice Hall
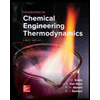
Introduction to Chemical Engineering Thermodynami…
Chemical Engineering
ISBN:
9781259696527
Author:
J.M. Smith Termodinamica en ingenieria quimica, Hendrick C Van Ness, Michael Abbott, Mark Swihart
Publisher:
McGraw-Hill Education
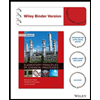
Elementary Principles of Chemical Processes, Bind…
Chemical Engineering
ISBN:
9781118431221
Author:
Richard M. Felder, Ronald W. Rousseau, Lisa G. Bullard
Publisher:
WILEY
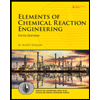
Elements of Chemical Reaction Engineering (5th Ed…
Chemical Engineering
ISBN:
9780133887518
Author:
H. Scott Fogler
Publisher:
Prentice Hall
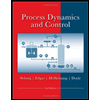
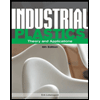
Industrial Plastics: Theory and Applications
Chemical Engineering
ISBN:
9781285061238
Author:
Lokensgard, Erik
Publisher:
Delmar Cengage Learning
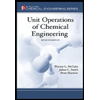
Unit Operations of Chemical Engineering
Chemical Engineering
ISBN:
9780072848236
Author:
Warren McCabe, Julian C. Smith, Peter Harriott
Publisher:
McGraw-Hill Companies, The